Cutting system
The cutting system automates pelletizer speed based on die head pressure, ensuring uniform pellet size. A pneumatic blade clamping device enhances blade precision and longevity.
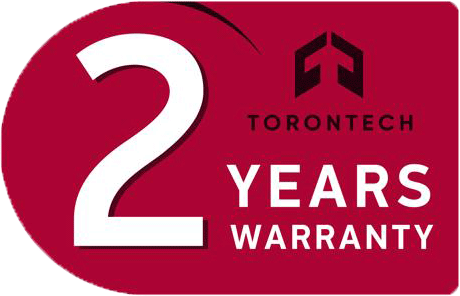
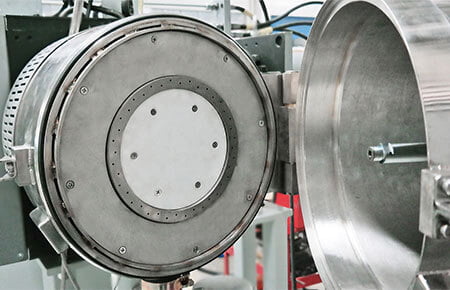
Water-ring cutting system
The pelletizer speed is automatically adjusted according to the pressure of the die head, ensuring consistent final pellet size. A pneumatic blade clamping device enables the pelletizing system's knife to compact with the die head automatically via a pneumatic system. This setup guarantees 100% contact between the blade and the pelletizing template, enhancing blade concentricity and prolonging its abrasion time.
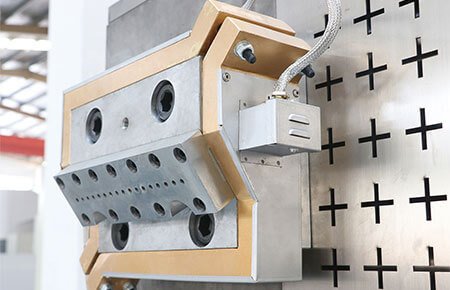
Water-strands pelletizing
The strip is manually pulled into the water tank for cooling. Once it exits the water tank, a wind knife removes the water from the strip's surface. The granulator pulls the strip and a hob cuts it for granulation. This traditional strip pelletizing method relies heavily on manual intervention and demands skilled operation. It's suitable for medium yield operations (less than 600 kg/h) involving pelletizing.
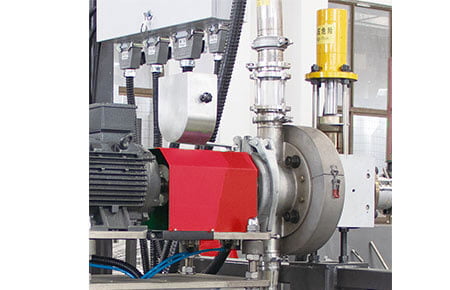
Under-water cutting system
The underwater granulator is specifically engineered to handle various polymers and thermoplastics, ensuring consistent spherical particles for subsequent production. It achieves an output capacity of up to 12,000 kilograms per hour and offers both manual and automatic operation modes. Its integrated water treatment system features a robust centrifugal dryer, ensuring complete particle-water separation and thorough drying while maintaining stable flow and temperature for the granulation process. This design offers flexibility and efficiency, accommodating installation on the ground, track, or as a pillar suspension. Tailored turnkey engineering solutions are available, covering aspects like factory layout, upper feeding systems, gravity metering devices, extruders, melt pumps, mesh changers, granulation and water treatment units, particle screening and separation units, and more, based on specific customer requirements.
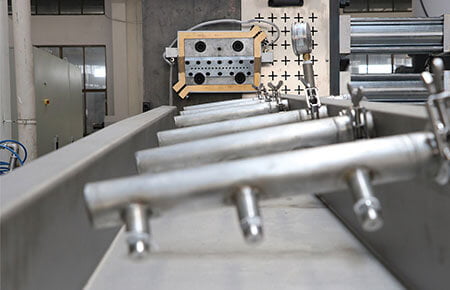
Automatic strands Cutting
To ensure stable and automated operations for high-yield processes, an automatic strip-slitting device with enhanced automation and continuity is essential for regenerating and granulating high-yield MFI materials. Unlike traditional drawing and granulating systems, this setup offers heightened automation, freeing the production process from strict manual operation requirements and eliminating the need for redrawing broken strips. This significantly boosts production line efficiency. The granulation section utilizes a water-cut granulator, safeguarding cutting tools and extending their lifespan. The system enables automatic stripping, granulation, screening, dehydration, and packaging of finished products, maintaining the moisture content of finished products at 1%.
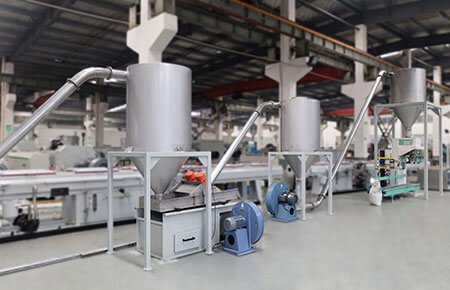
Hot -face cutting
A hot-face cutting machine is equipped with a multi-hole die plate at the extruder's end, with all cutter discs fixed on the extension end of the screw spindle that passes through the die plate. Each cutter disc is closely attached to the multi-hole die disc, with the cutter's length corresponding to the radius of the multi-hole die disc. A cylindrical compression spring is installed on the outer extension end of the screw spindle. One end of the spring compresses the cutter disc, while the other end is supported by a coupling at the end of the screw spindle. The device, including the porous formwork and cutter disc at the extruder head, is enclosed within a hood. This hood is connected to the air supply pipe of a high-pressure fan, and its lower end is equipped with an outlet.