Plastic PET Bottles Washing and Pelletizing line
Plastic PET Bottles Washing and Pelletizing line - Plastic, as a renewable energy source, holds the potential for sustainability through closed-loop regeneration. Our solution prioritizes low energy consumption while maintaining high-grade standards. It has the capability to recycle discarded beverage bottles to meet food-grade standards. Our recycling technology creates a significant impact in this regard.
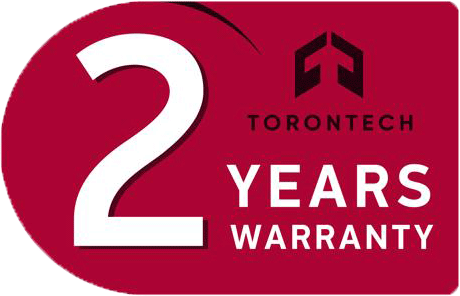
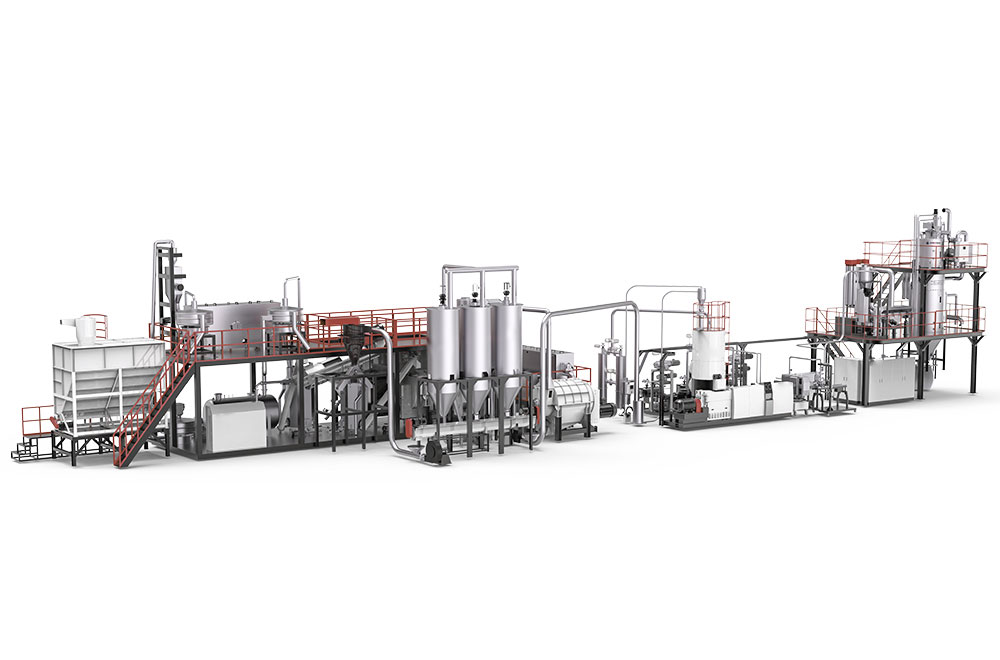
Easy Recycling and Valuable Plastics
Plastic, as a renewable energy source, holds the potential for sustainability. We achieve closed-loop regeneration. Our solution is crafted with low energy consumption and adheres to high-grade standards. We have the ability to recycle discarded beverage bottles to meet food-grade standards, and our recycling technology creates a significant impact.

Provide Complete Solutions
-- Bottle and sorting system
-- Washing line
-- Pelletizing system
-- Viscosity increase system
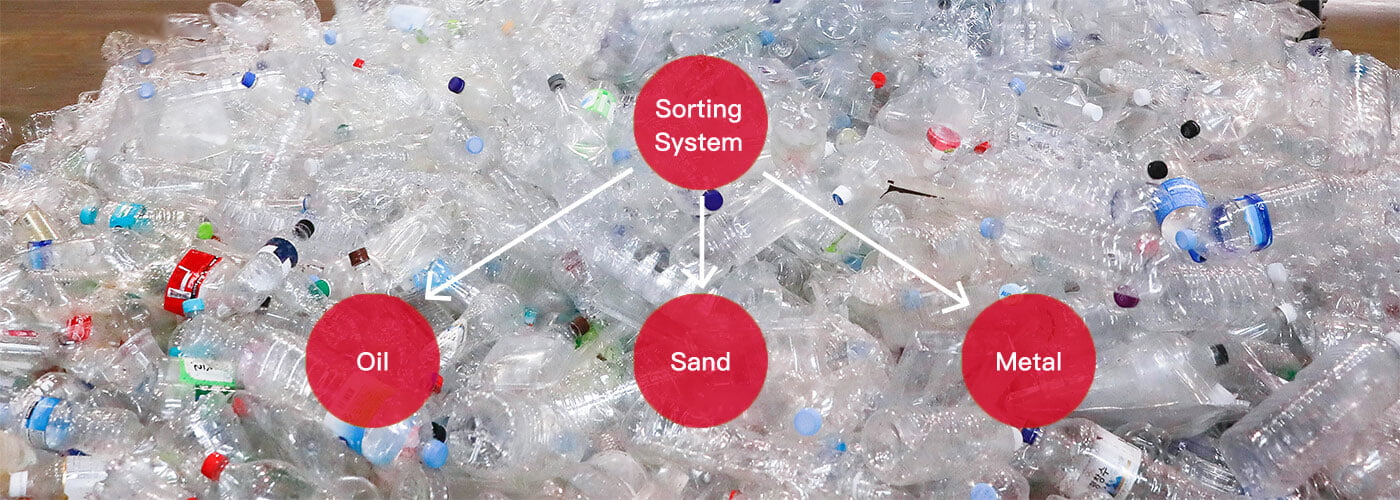
Bottles and Sorting System
-- Pre-sorting the incoming material.
-- Separation of foreign matter and impurities, sorting the input material.
-- Separation of containers.
-- Removal of undesired foreign matter and impurities such as wood, sand, glass, metal, colored plastic materials, and foreign polymers.
-- Label removal.
-- Crushing into flakes.
The pre-sorting system can be customized to suit the quality of the incoming material, local conditions, and the desired purity levels.
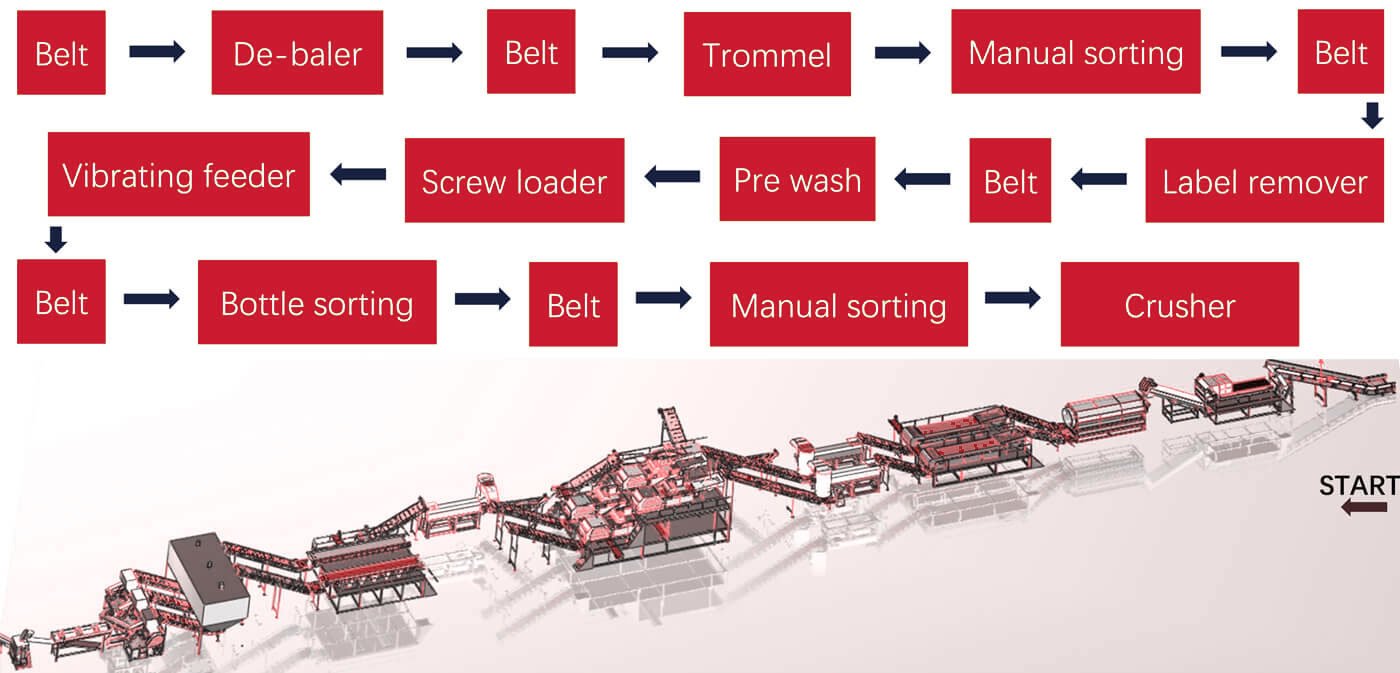
Bottles and Sorting System
- Belt De-baler
- Belt Trommel
- Manual sorting Belt
- Belt Pre-wash
- Screw loader
- Vibrating feeder
- Belt Bottle sorting
- Belt Manual sorting
- Crusher
- Label remover
Producing PET pellets for high-grade applications demands precise recycling solutions. In the initial stages of pre-processing, we carefully select high-quality bottles and eliminate impurities such as sand and wood.
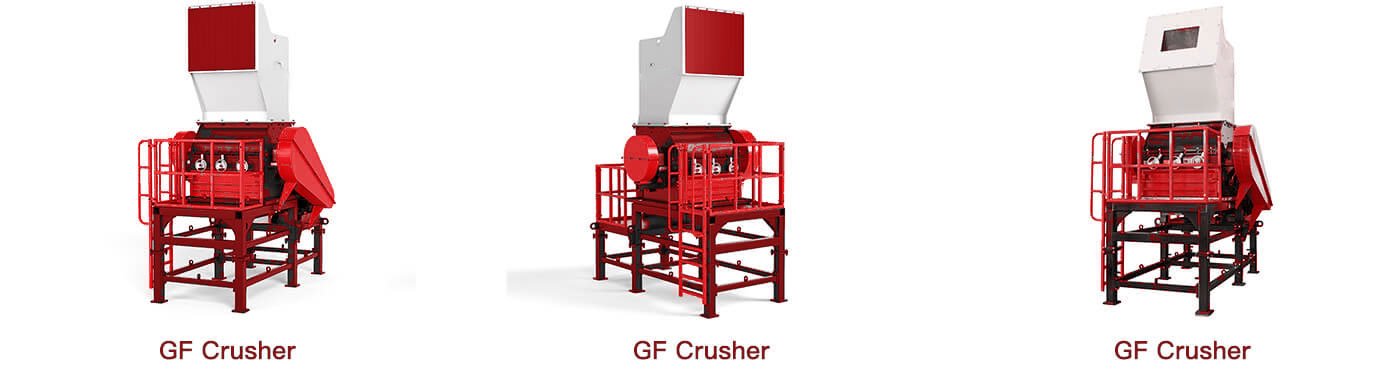
Crusher
* Increased throughput with lower power consumption, thanks to the optimal geometry of the rotor and cutting chamber.
* Ideal rotor knife mounting for heavy-duty applications and enhanced cutting power.
* Improved granule shape for better quality cuts and reduced noise levels attributed to precise cutting gaps and optimal rotor design.
* Hydraulic system enabling heavy-duty, stronger push power.
Washing Line
Washing process incorporates pre-treatment, caustic washing, and hot post-washing to yield clean flakes ideal for high-quality applications such as fiber, film, and injection molding.

- Pre-washing
- Caustic cleaning with caustic renewal
- Multi-stage post-washer
- Drying
- Automatic waste management system to reduce operator workload
- Separation of labels and caps using a float-sink separation system and sifter
Pelletizing System
- Vacuum Loader
- Vacuum-state sliding gate feeding device
- Vacuum pump units and dust filtering system
- Reactor with 5-layer combined cutter discs
- Single screw extruder
- Backflush screen changer
- Melt pump
- Melt viscosity online measurement system
- Automatic Underwater Pelletizing system
- Packing system
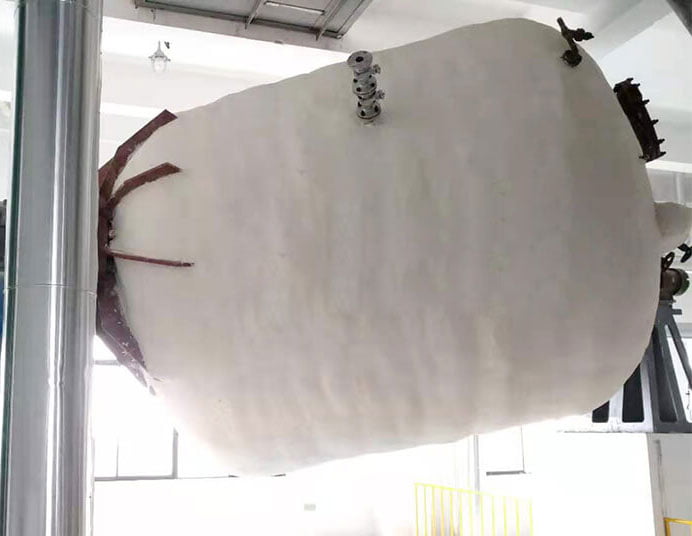
Viscosity Increase System -- SSP
Our latest efficient recycling solution incorporates vacuum technology, SSP IV increasing technology, and a specially designed pelletizing extruder. This ensures that the IV value of the final PET granules meets set requirements and is consistently maintained. Even with variations in IV values and raw material moisture content, the pellets consistently maintain a qualified IV value within a specified range. This stability in quality and output is constant, facilitating a steady IV value output for downstream processing and molding, such as stretch blow molding, enabling up to 100% bottle-to-bottle technology for new bottles.
Compared to bottle flakes, particle viscosity offers advantages such as uniform particle size and absence of powder, resulting in a consistent final viscosity.

Viscosity Increase System -- LSP
The LSP equipment is suitable for processing various materials such as PET film, sheet, scrap, perforated waste, fabric fibers, polyester cloth, waste silk, and more. Its key features include the Spray Cooling Vacuum Exhaust Device and the Multi-screw Large Area Vacuum Exhaust Extruder. Compared to standard exhaust devices, the spray cooling vacuum exhaust device enhances the empty surface area of PET melt by up to 1000 times. Additionally, the multi-screw large area vacuum exhaust extruder not only increases the PET melt surface area but also achieves PET homogenization. When combined with a robust vacuum pump, these devices effectively eliminate glycol from PET and enhance the melt's polymerization degree. This process facilitates the production of new PET molecules, ultimately increasing the intrinsic viscosity (IV) of PET.
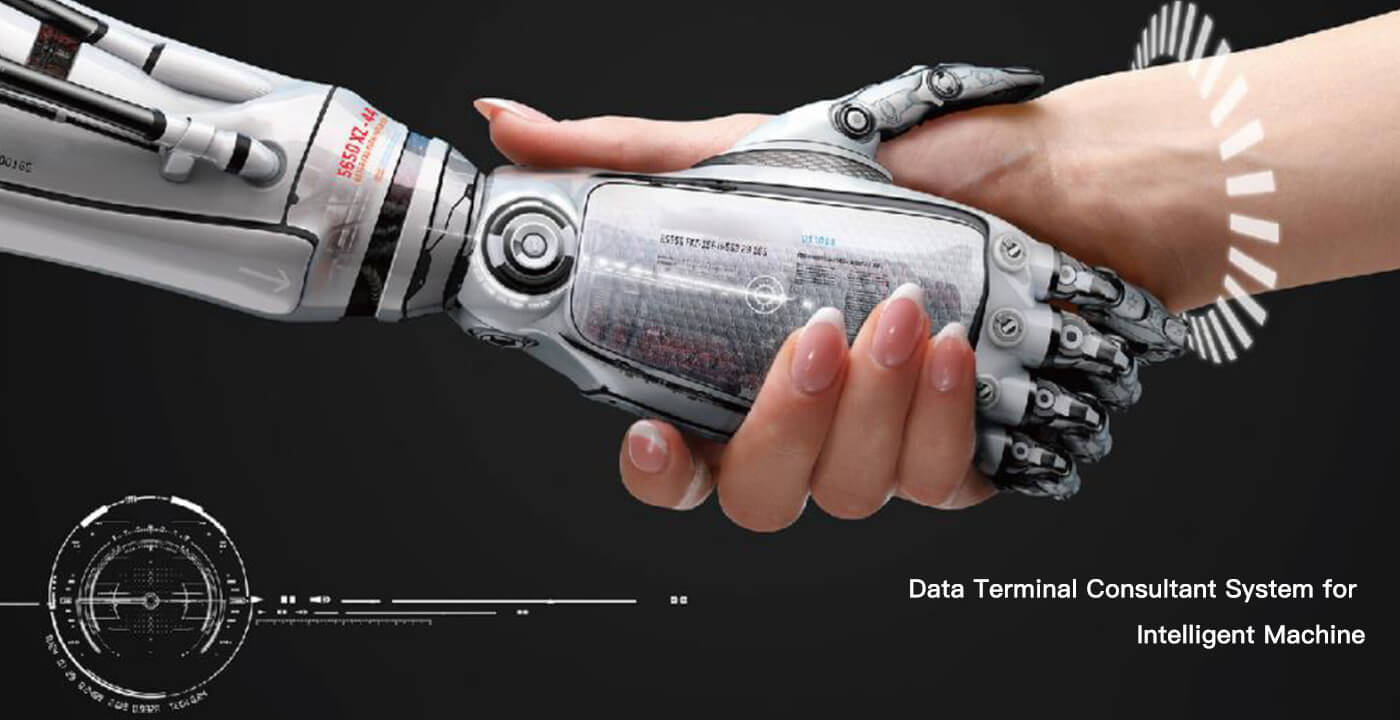
Data Terminal Conusltant System For Intelligent
The machine integrates digital processes for equipment maintenance, encompassing functionalities like automated notifications for planned maintenance, swift creation of work orders for equipment repairs, and timely execution of maintenance tasks. Every step of execution and processing is relayed online and in real-time via short messages, ensuring efficient equipment maintenance and minimizing downtime. This approach optimizes time, enhances production efficiency, and maximizes equipment utilization. Additionally, it supports data analysis and decision-making processes. The system provides production operation indicators such as equipment failure rates promptly, enabling timely insights. Equipment maintenance data can be rapidly analyzed and summarized, facilitating informed business decisions for management.
What can we do for you?
We offer comprehensive washing and pelletizing turnkey solutions for all our customers. Please get in touch with our professional sales team Contact Torontech, and they will tailor customized solutions for your needs. We can provide design drawings and technical specifications according to your specific requests.
Installation, Testing and Training
We can arrange engineers to visit customers' factories for installation, testing, and training as per your requirements. This process ensures smoother integration of the new machine into the factory setup. Our engineers can conduct training sessions at the customer's factory during installation, and customers are also welcome to send their engineers for training. Our technicians will comprehensively cover operational and maintenance aspects of the equipment for the customer's engineers. Detailed instruction manuals will be provided to all customers, facilitating convenient operations. Prior to delivery, we will offer layout drawings and installation requirements, aiding operators in thorough preparation for production and enhancing operational efficiency. Please contact sales to arrange on-site work and support.
Spare Parts
We maintains a stock of spare parts, and our efficient service staff ensures prompt shipping of any required parts without delay. Spare parts can be transported by air, sea, or courier depending on the urgency. We encourage our customers to maintain their own key spare parts, such as pelletizing blades and rubber seals, to ensure optimal machine conditions and production performance in case of any delays in spare parts delivery.
Service Support
Your sales representative will offer professional consultation, ongoing service, and spare parts assistance.
Our Dream
Through our solution, we aim to restore the value of waste plastics for human use rather than contributing to environmental issues, simplifying and streamlining the entire recycling system.