Metallurgical Image Analysis Software - ToronMat+™
Metallurgical Image Analysis Software - ToronMat+™ is built for professionals working with industrial materials—scientists, metallurgists, lab technicians, and R&D engineers—who require advanced tools for quality control and product development.
Elevate your analysis with ToronMat+™, the smart imaging solution built to meet ISO and ASTM standards.
Compatible with major image formats and a wide range of imaging devices, ToronMat+™ captures up to 80% more detail than conventional tools. Its advanced features make image capture, enhancement, and measurement more efficient and accurate—while the live measurement tool accelerates your workflow.
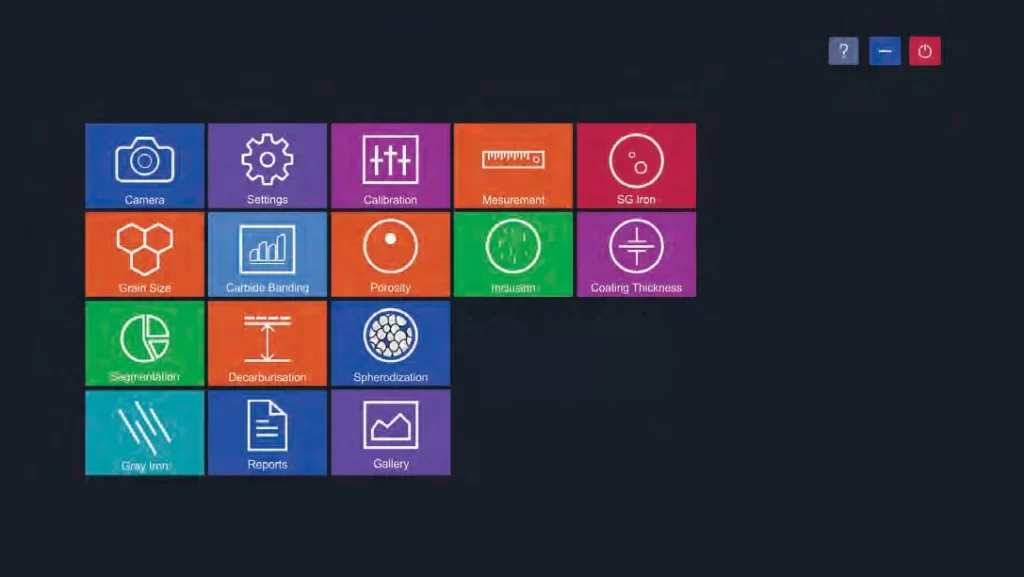
Key Modules in ToronMat+™ Metallurgical Image Analysis Software
CAMERA
Live image parameters—such as white balance, brightness, contrast, hue, and saturation—can be precisely adjusted. Captured images are then stored in a designated folder for further analysis.
CALIBRATION
Calibration must be performed for each microscope objective paired with a digital camera. It should only be carried out after all hardware components are fully secured. Recalibration is required if any component is readjusted or replaced.
MEASUREMENT
The module allows precise measurement of manually drawn lines, shapes, and outlines. Results are automatically documented in a worksheet and can be saved, printed, or exported for extended analysis and statistical processing.
GRAIN SIZE
The Grain Size module provides fast, consistent evaluations of ferritic and austenitic grain sizes in steel. Analysis follows ASTM E112, E93, and E1181 standards for accuracy and repeatability.
POROSITY
This module analyzes porosity using grayscale thresholding to detect contrast variations. Porous regions are identified according to ASTM B276, with dark phases highlighted in red bitplanes for clear visualization.
SEGMENTATION
Image segmentation by grayscale intensity enables multi-phase detection. A histogram-based tool supports accurate phase separation, with colored overlays providing simultaneous phase visualization.
DECARBURIZATION
This module evaluates the depth of decarburization by detecting structural changes and identifying ferrite boundaries. It distinguishes between partial and full decarburization zones in accordance with ASTM E1077-91.
SG IRON (Ductile Iron / Spheroidal Graphite Iron)
Designed for ductile iron analysis, this module evaluates graphite nodules formed during solidification. It adheres to ASTM A247-67 and ISO 945-1 standards.
GRAY IRON
Tailored for gray cast iron, this module analyzes the graphite-rich microstructure using methods outlined in ASTM A247-67 and ISO 945-1.
CARBIDE
This module identifies and evaluates iron carbide (cementite), a common intermetallic compound in steels and cast irons, also used in alternative ironmaking processes.
COATING THICKNESS
Plating or coating thickness is measured via cross-sectional microscopy. The sample is sectioned, mounted, polished, and, if necessary, etched. Measurements are based on optical examination of metal and oxide layers.
SPHEROIDIZATION
This module distinguishes spheroidal graphite nodules from irregular shapes. Nodules are marked in blue, non-nodules in red. Nodules are classified by type (I–VI) and size (1–8), with nodules per mm² calculated for completeness.
INCLUSION ANALYSIS
Detects and classifies four types of non-metallic inclusions:
- Sulfide Type (A)
- Alumina Type (B)
- Silicate Type (C)
- Globular Type (D)
Each inclusion is categorized as Thin or Heavy based on its width.
SETTINGS
Configure software preferences including ISO/ASTM standards, report formats, and image display options. Once set, analyses can be run with a single click. These configurations persist unless changed manually, so frequent updates are not needed.
REPORTS
All analytical reports are automatically saved and easily accessible. Report categories include:
- Measurement
- Grain Size
- Porosity
- Decarburization
- Segmentation
- SG Iron
- Gray Iron
GALLERY
Captured images are sorted into clearly labeled folders for quick access. Available categories include:
- Nodularity
- Flake
- Carbide
- Line Measurement
- Grain Size
- Porosity
- Decarburization
- Segmentation
- SG Iron
- Coating Thickness
Camera
Users may select desired display and capture resolutions and adjust live settings—including white balance, brightness, contrast, hue, and saturation. Configured images are then saved automatically to a designated folder for further analysis.
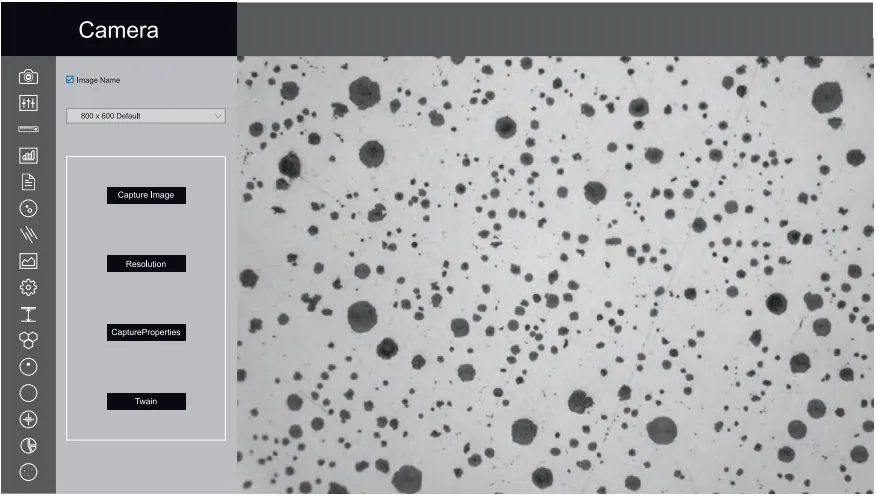
Calibration
Each microscope objective used with a digital camera requires calibration, which should be completed after full hardware installation. Any adjustment or replacement of components necessitates recalibration.
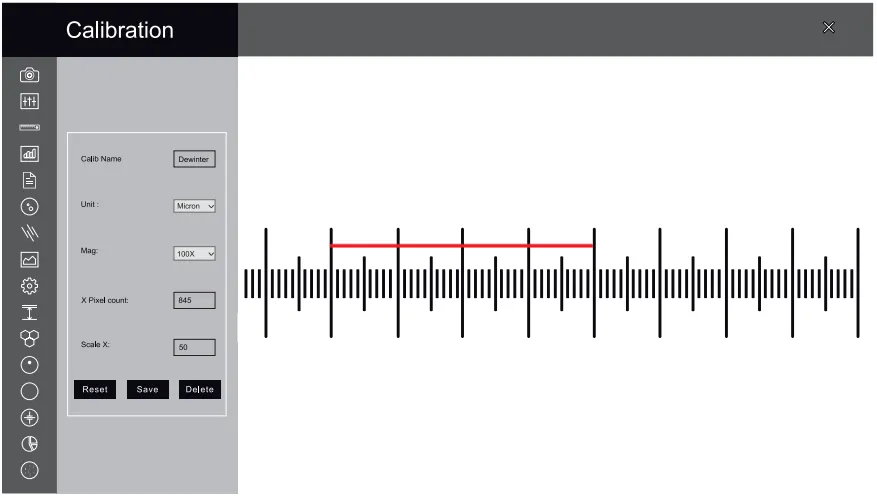
Measurement
Gain precise measurement control with the Measurement module—draw directly on traces, shapes, or outlines, and instantly record results in a worksheet. Export, print, or save your data for easy analysis and reporting.
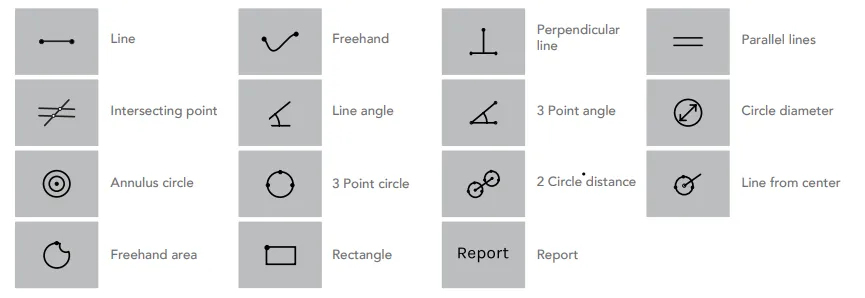
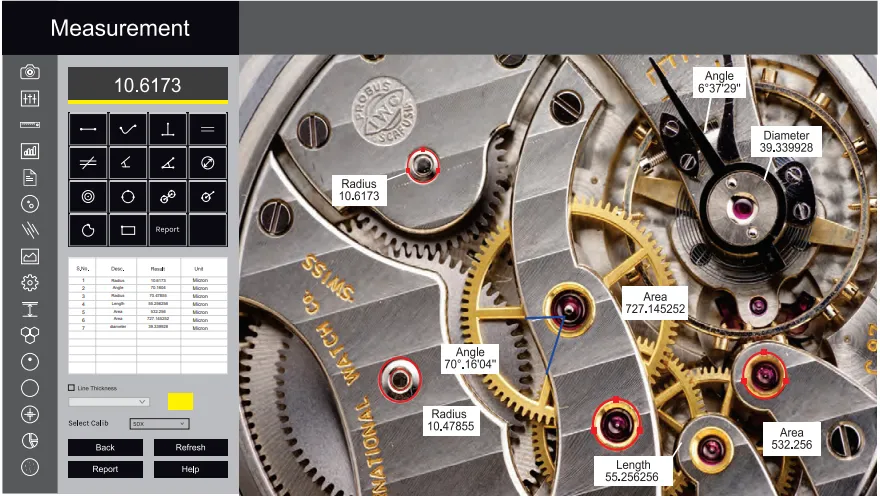
Grain Size
The module enables fast, reliable, and repeatable grain size analysis compliant with standards like ASTM E112, E93, and E1181. It supports assessment of both ferritic and austenitic steel grain structures.
A comprehensive set of analysis techniques is included:
- Lineal Intercept Method
- Abrams Three-Circle Method
- Snyder & Graft Method
- Comparison Method
- Random Intercept Method
- Manual Grain Size
The built-in analysis wizard quickly calculates grain number, mean grain area, and mean intercept length based on the selected method.
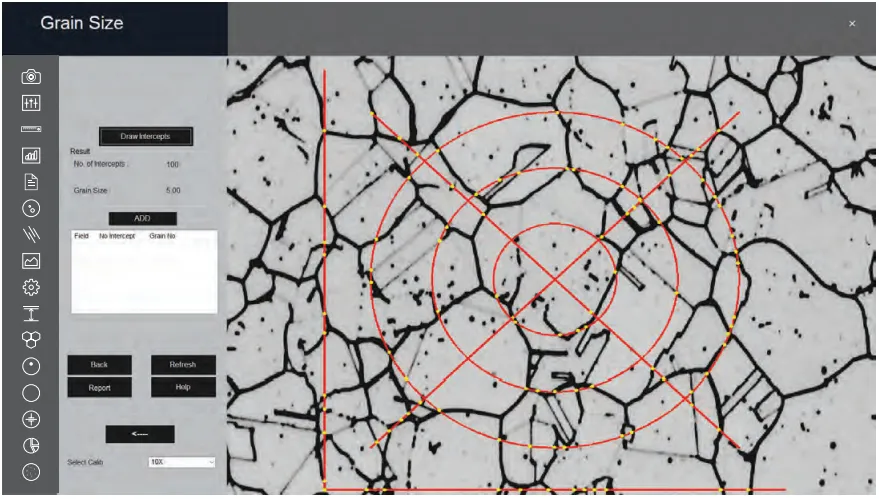
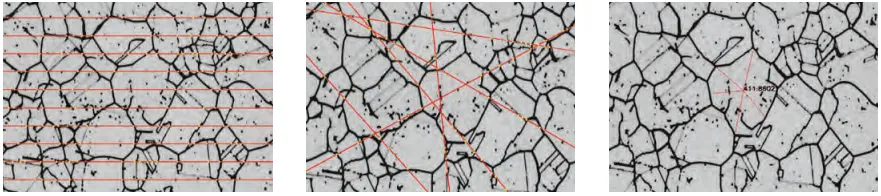
Segmentation
The Segmentation module identifies and quantifies material phases by partitioning images based on grayscale intensity. Users define phases via a histogram, ensuring accurate detection.
Each phase is displayed with a unique color overlay, allowing simultaneous visualization. Preprocessing filters like Despeckle and Smoothing enhance accuracy. Both segmented images and data are saved for clear phase analysis.
HISTOGRAM
Upon launching the module, a grayscale histogram is automatically generated. The X-axis represents intensity values (0–255), while the Y-axis shows the number of pixels at each level. The system supports standard industry analysis.
Users can define up to ten threshold levels to identify and label different phases, with each phase assigned a unique color between the selected thresholds.
INTENSITY DISPLAY
The current intensity range of the selected phase is shown in real time within the dialog box, allowing for quick adjustments and precise control.
SELECTED PHASE ANALYSIS
By clicking within the histogram, users can determine the percentage area of a specific intensity range. For accurate results, previous selections must be cleared, and preview mode should be set to “None.”
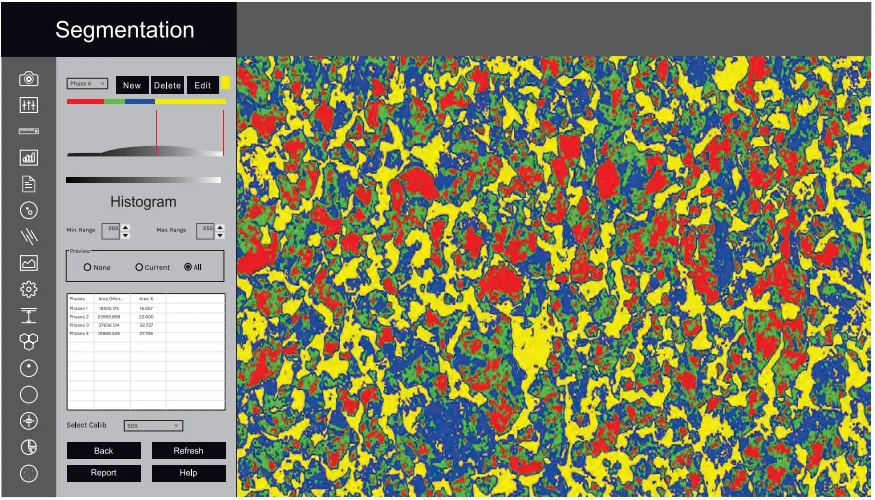
Porosity
Due to distinct contrast, pores are readily identified. This module applies grayscale thresholding for automatic porosity analysis in compliance with ASTM B276. Pores appear as red-highlighted regions within bitplanes for clear visibility.
The system reports total pore count and detailed size distribution, including min/max values as percentages. The process is fully automated, delivering consistent and precise results.
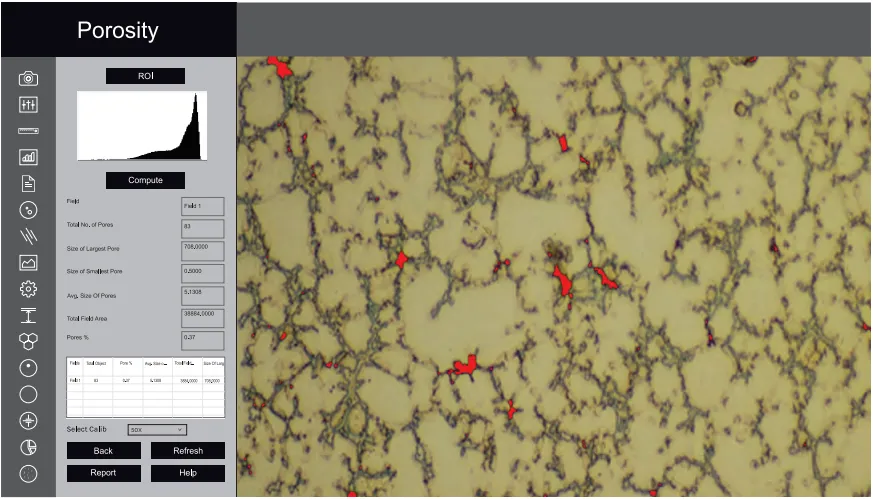
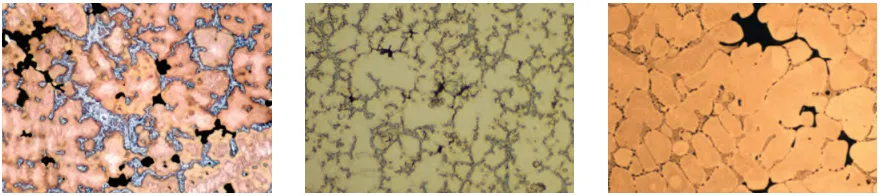
Ductile Iron/Nodularity
Ductile Iron—also referred to as Nodular Cast Iron, Spheroidal Graphite Iron, or SG Iron—is a type of cast iron characterized by its graphite-rich microstructure. This module utilizes advanced image processing techniques, including global thresholding, boundary detection, and artificial neural networks, to deliver accurate microstructural analysis.
Nodules touching image boundaries are excluded, and any features smaller than 10 microns are automatically filtered out. Nodules and non-nodules are classified based on predefined spheroidicity parameters.
Automated Measurements Include:
- Nodule Count
- Nodule Size (classified using Arabic numerals 1 to 8)
- Nodule Form (classified using Roman numerals I to VI)
All measurements are completed automatically with a single click.
In the second phase of analysis, etched samples are evaluated. The system calculates the percentage of Graphite and Pearlite present in the structure. Results from both etched and non-etched samples are compiled directly into a spreadsheet within the software interface.
Comprehensive reports—with detailed data and associated images—are generated instantly with one click.
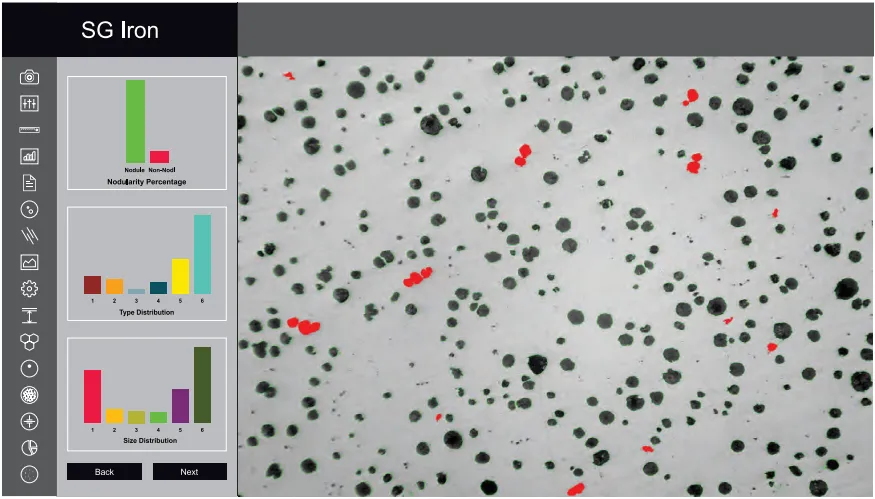
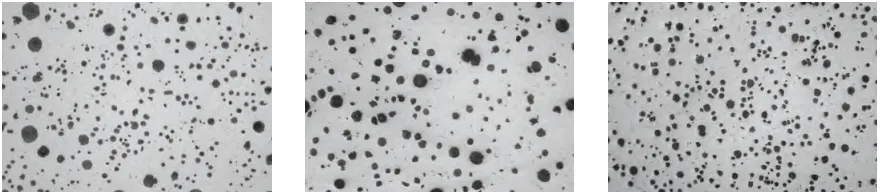
Ductile Iron/Nodularity
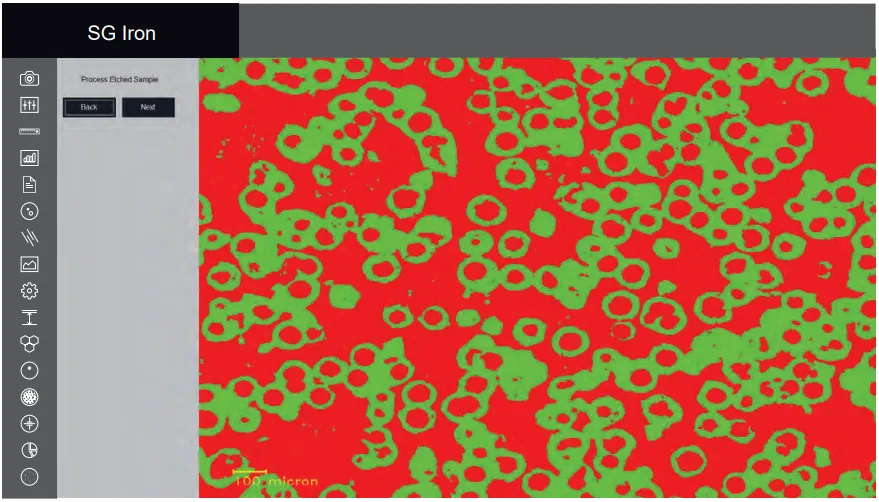
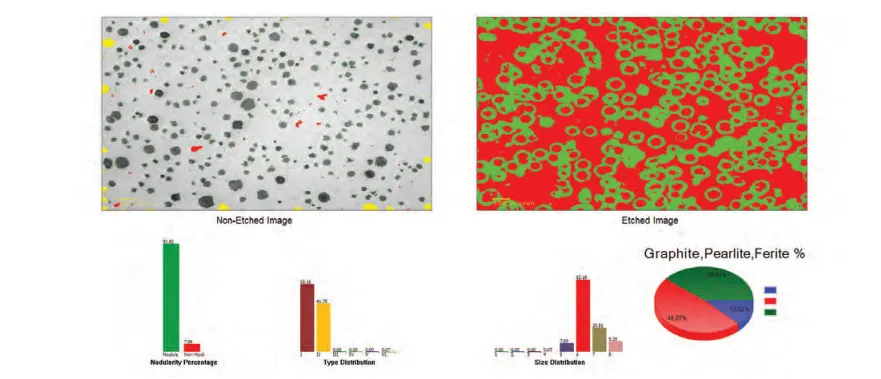
Gray Iron/Graphite Flakes
Gray Iron, or Gray Cast Iron, features a graphite flake microstructure that forms during solidification. Its name derives from the gray appearance of its fracture surface, caused by the presence of graphite.
This module automatically analyzes graphite flakes in gray iron samples using advanced metallographic imaging. Short Type A flakes are typically associated with higher strength and better ductility.
With a single click, the software measures:
- Graphite Flake Length (classified into eight size classes: 1–8)
- Graphite Types (A, B, C, D, E) based on flake orientation and distribution
The analysis complies with ASTM A247-67 and ISO 945-1 standards.
In etched samples, the software calculates the percentage of pearlite by excluding the graphite phase. The final report includes a breakdown of the matrix composition, detailing the proportions of pearlite, ferrite, and graphite.
Detailed reports are auto-generated based on the chosen international standards.
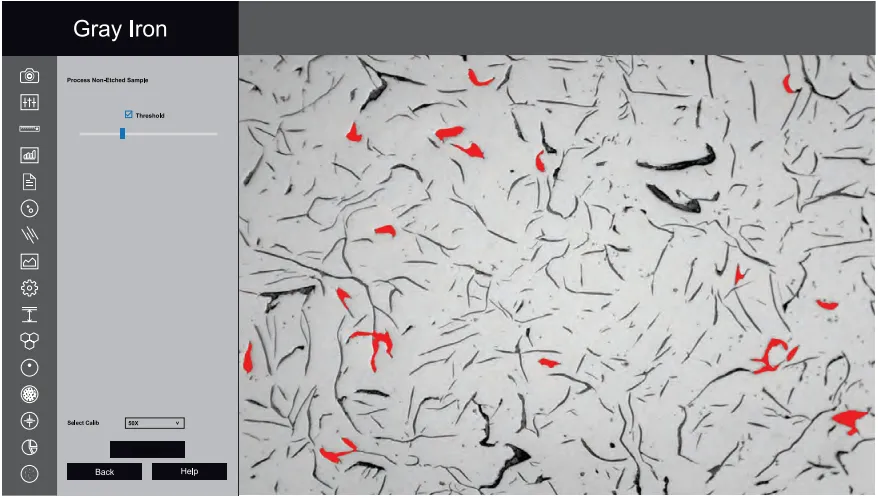
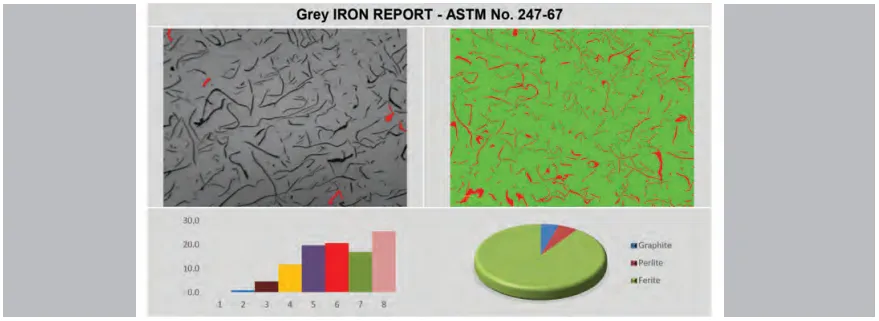
Decarburization
The module evaluates decarburization depth by detecting microstructural variations. Partial decarburization reflects carbon loss without full depletion; complete decarburization reaches the ferritic boundary.
Measurements along the cross-section are accurate and fully compliant with ASTM E1077-91.
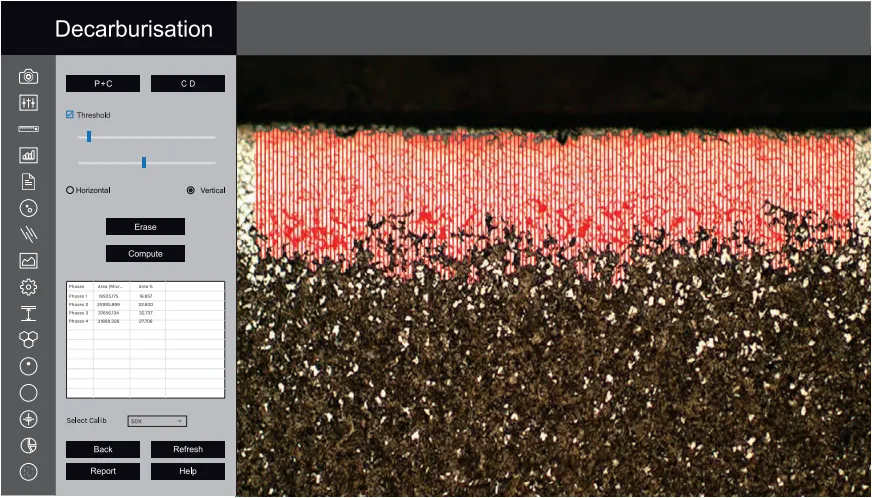
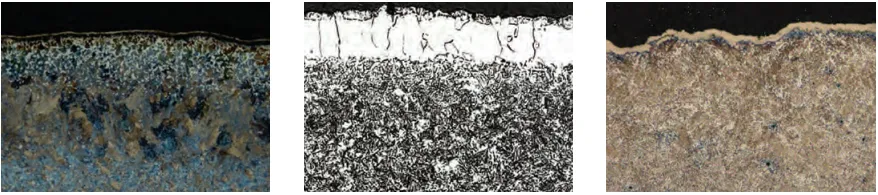
Coating Thickness
This module measures plating or coating thickness using a cross-sectional microscopy method. The specimen is sectioned, mounted, polished, and examined under an optical microscope. In some cases, etching the base metal is required to enhance contrast and clearly define the coating layer.
The method evaluates the local thickness of both metal and oxide coatings through precise optical measurement. Under optimal conditions, the system can achieve an accuracy of up to 0.8 microns, making it ideal for analyzing thin coatings with high precision.
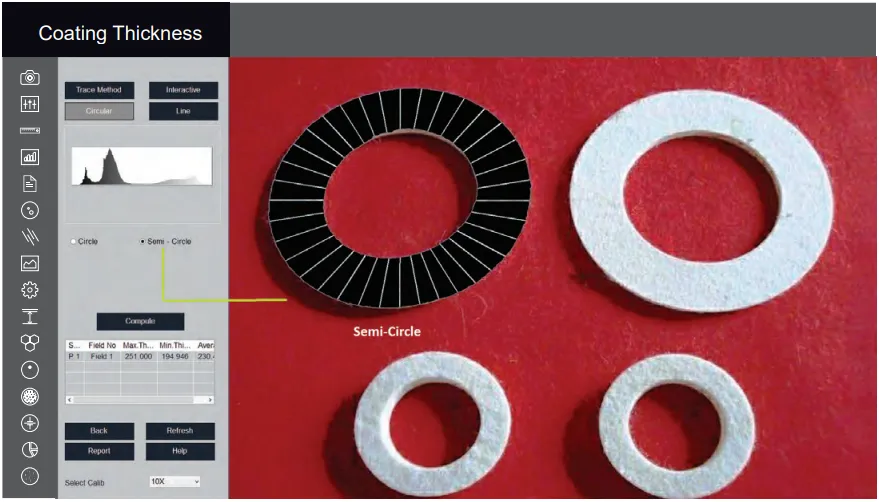
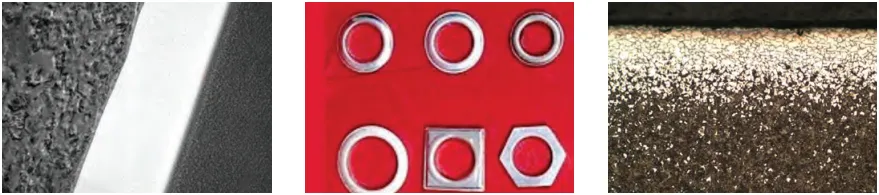
Spherodization
This module analyzes spheroidal graphite (nodules) in cast iron samples, classifying features based on predefined spheroidicity criteria. In the visual output, nodules are highlighted in blue, while non-nodules appear in red for easy identification.
Each nodule is automatically classified by:
- Form (Roman numerals I to VI)
- Size (Arabic numerals 1 to 8)
The software also calculates the nodule density, expressed as nodules per square millimeter (nodules/mm²), providing valuable insight into the material's structural quality.
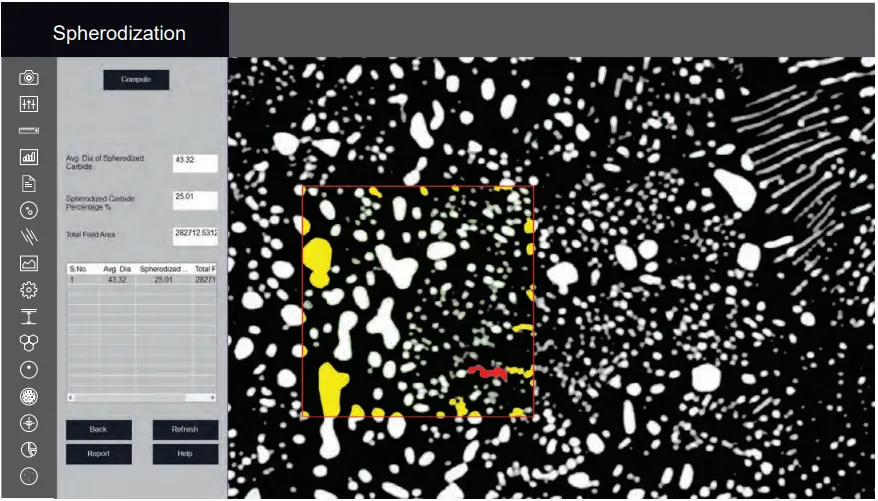
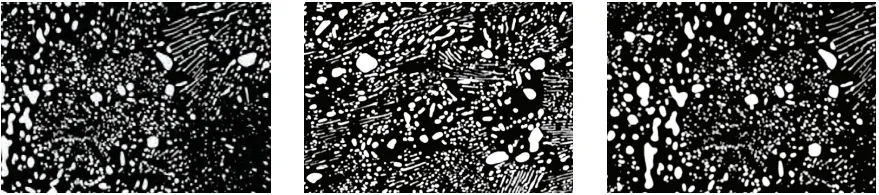
Carbide Banding
Iron carbide, or cementite, is an intermetallic compound composed of iron and carbon. It naturally forms in steels and cast irons as part of the microstructure. In addition to occurring during conventional processing, iron carbide can also be produced as a raw material through the iron carbide process, an alternative iron-making technology.
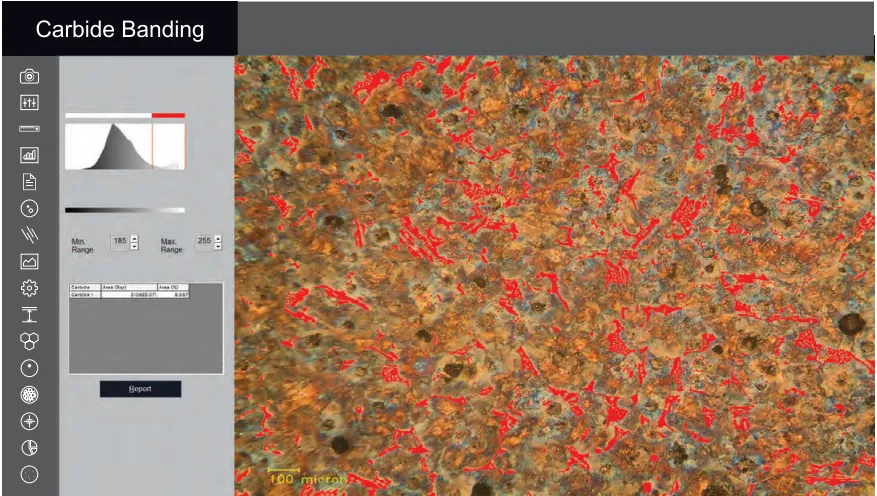
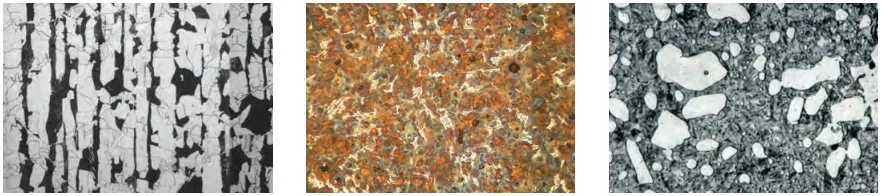
Non Metallic Inclusion
ToronMat+™ software enables the detection and classification of four types of non-metallic inclusions in metallographic samples:
- Sulfide Type (Type A)
- Alumina Type (Type B)
- Silicate Type (Type C)
- Globular Type (Type D)
Each inclusion type is further categorized as Thin or Heavy, based on width characteristics. This classification supports consistent and accurate evaluation of material purity and quality.
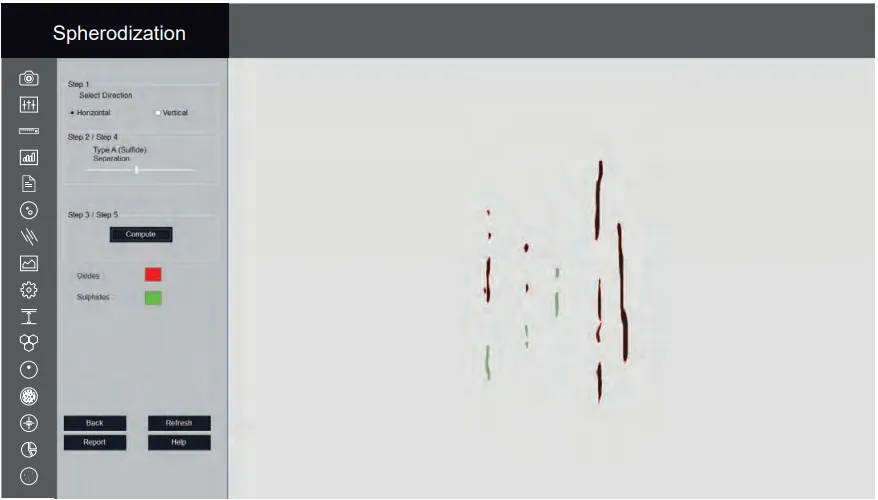
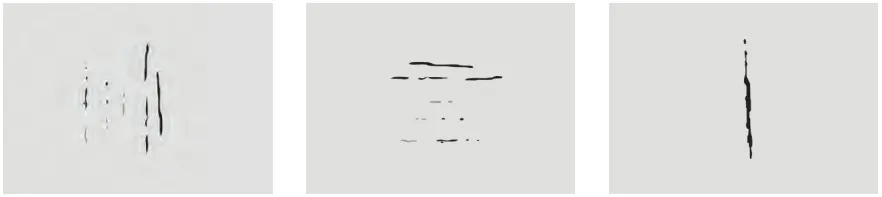
Settings
The Settings module allows users to configure key parameters during the initial setup of ToronMat+™ software. Options include:
- Selecting ISO/ASTM calibration standards
- Customizing the report format
- Defining which parameters appear on printed report images
Once configured, a single click applies the saved preferences to all analyses. These settings are stored permanently and only require updates if there are changes in standards or specific application requirements.
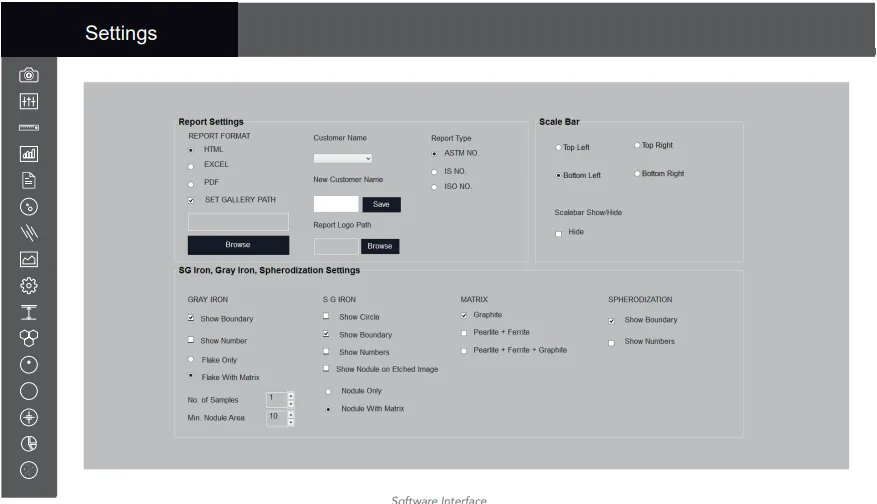
Clicking the Settings icon opens a dedicated interface designed to streamline your workflow. By selecting the appropriate options using radio buttons and checkboxes, you can reduce errors and enable one-click operation across the software.
1. Report Type
Select your preferred reporting standard:
- ASTM
- ISO
Your selection is saved as the default until manually changed.
2. Set Default Workflow
Choose how you'd like to perform your analysis:
- Live Display – Analyze images in real time.
- Stored Images – Capture images first, analyze them later.
3. Select Calibration
Pick from preloaded calibration settings.
For Cast Iron analysis, the 100X objective is typically used.
4. Set 100 Micron Scale Bar
Customize image overlays:
- Enable Show Boundary to outline graphite features.
- Enable Show Number to display count labels.
5. Set Gallery Path
The gallery path is preconfigured but can be modified to suit your storage preferences.
6. SG Iron Options
Control the display of SG Iron analysis data.
If no specific settings are applied, a default contour will be generated.
7. Aspect Ratio
Usually fixed—adjust only if explicitly required for your analysis setup.
8. Report Template Options
Choose between two template formats:
- With chemical composition and physical properties
- Without chemical and physical data
Gallery
ToronMat+™ provides quick and organized access to captured images through categorized folders. Each folder corresponds to a specific analysis type, making it easy to locate and review past work.
Available folders include:
- Measurement
- Segmentation
- Grain Size
- Porosity
- Decarburization
- SG Iron
- Gray Iron
This structured gallery system streamlines image management and supports efficient data review.
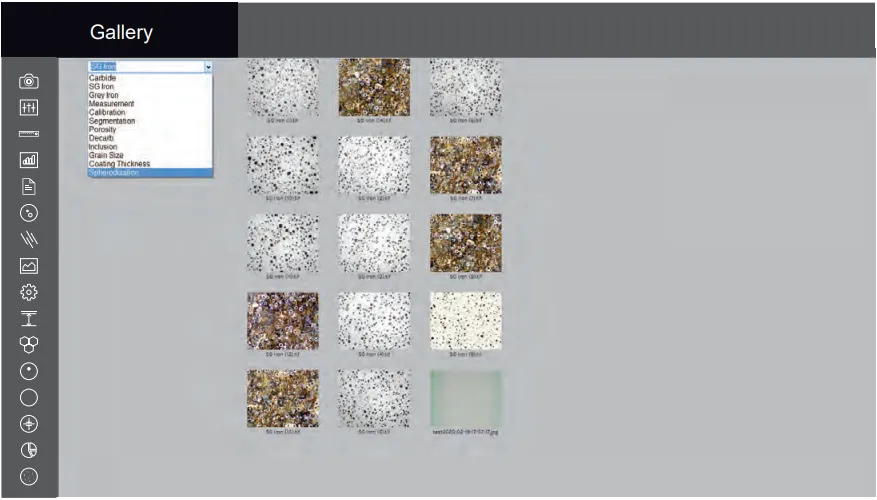
Save Report
All reports are saved to a designated folder and can be retrieved at any time for future reference.
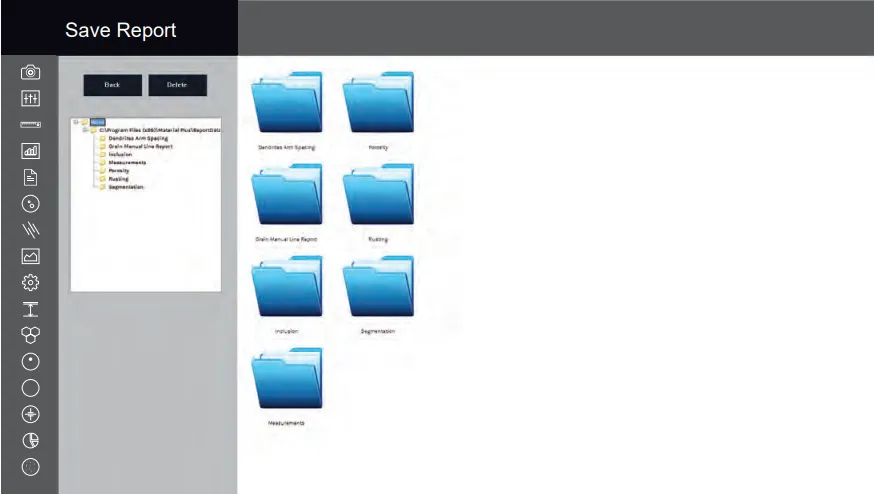
Please Contact us for pricing, check availability, or ask for additional information about our Metallurgical Image Analysis Software – ToronMat+™