Sputter Coaters / Vacuum Coating Systems
Torontech offers an extensive range of desk sputter coater and vacuum coating systems. These Sputter Coater and Vacuum Coating Systems span from low to high-vacuum sputter coaters such as the DSR1 and DST1, which are commonly used for sample preparation in electron microscopy imaging, to high-vacuum sputter coater and thermal evaporator systems like the DST2-TG or DST3-T. These systems come with a variety of optional features, including a plasma cleaner, primarily intended for thin film deposition for research purposes.
Our engineering team designs and manufactures Sputter Coater and Vacuum Coating System components that adhere to high-quality standards. Many prestigious universities and research centers count among our valued customers, all of whom have expressed satisfaction with this advanced range of sputter coater and vacuum coating systems.
Product Categories
Desk Carbon Coater - DCR
Desk Carbon Coater - DCR is a compact carbon fiber coating system suitable for sample preparation for the use in scanning electron microscope (SEM), Transmission electron microscope (TEM) and X-Ray analysis (EDX).
Desk Sputter Coater- DSR1
The Desk Sputter Coater - TT-DSR is able to coat noble metals, such as Gold (Au), Silver (Ag), Palladium (Pa) and Platinum (Pt) thin films on non-conductive or poorly conductive specimens uniformly and fine-grain size in...
High Vacuum, Single Magnetron Target Desk Sputter Coater DST1-170
High Vacuum Single Magnetron Target Desk Sputter Coater DST1-170 is perfect for SEM sample preparation, depositing materials like Au, Pt/Pd, Ag, Cr, W, and Ir. Produces high-quality films for FE-SEM, EDS/WDS, TEM...
High Vacuum, Single Magnetron Target Desk Sputter Coater DST1-300
High Vacuum Single Magnetron Target Desk Sputter Coater DST1-300 for semiconductors, dielectrics, and metals. 2-4 inch magnetron, 600W DC and 300W RF power. Ideal for specimens up to 15 cm, unlimited sputtering time.
Turbo Pumped Desk Carbon Coater - DCT
Turbo Pumped Desk Carbon Coater DCT for FE-SEM, EDS/WDS, TEM, EBSD, and thin film applications. Produces high-quality, uniform carbon films with fine grain sizes, ideal for high-resolution, top-quality characterization.
Desk Sputter & Carbon Coater - DSCR
Desk Sputter & Carbon Coater DSCR for noble metals (Au, Pd, Pt, Au/Pd) and carbon films. Features rotary pump, interchangeable heads, and user-friendly software for SEM sample preparation.
Desk Sputter & Carbon Coater – DSCR-300
Desk Sputter & Carbon Coater DSCR-300 with 3-4 inch water-cooled magnetron for large specimens up to 15 cm. Ideal for thin and thick layers, micro/nanoelectronics, and SEM prep. Handles noble metals and carbon films.
High Vacuum Desk Sputter & Carbon Coater - DSCT
High Vacuum Desk Sputter & Carbon Coater DSCT for SEM analysis. Features 2-inch magnetron, 80W DC power, and high current for carbon. Optional water-cooled cathode and higher-power supply for oxidizing metals.
High Vacuum Sputter Coater and Carbon/Thermal Evaporator – DSCT-T
High Vacuum Sputter Coater and Carbon/Thermal Evaporator DSCT-T for SEM prep. Features 3 interchangeable heads, deposits metals like Au, Pt/Pd, Ag, Cr, W, Ir. Ideal for FE-SEM, EDS/WDS, TEM, EBSD applications.
High Vacuum Thermal Evaporator - DTE
High Vacuum Thermal Evaporator DTE for research and electron microscopy. Compact, cost-effective system for thin layer deposition of materials under high-vacuum conditions, ideal for noble and oxidizing metals.
Desk Thermal Evaporator - DTT
Desk Thermal Evaporator DTT for vacuum thin film deposition. Triple-source capabilities (boats, baskets, coils) ideal for multilayer films or alloys. Reaches vacuum pressure quickly, perfect for lab research.
High Vacuum, Triple Magnetron Target Desk Sputter Coater - DST3-A/S
High Vacuum, Triple Magnetron Target Desk Sputter Coater DST3 is a desk top, triple target, turbo molecular vacuum pumped sputter coater, suitable for sputtering semiconductors, dielectrics, metals and metal oxides.
High Vacuum, Triple Magnetron Target Desk Sputter Coater with Thermal Evaporator - DST3-TA/S
High Vacuum Triple Magnetron Target Desk Sputter Coater with Thermal Evaporator DST3-TA/S. Versatile for thermal evaporation and sputtering, 300 mm chamber, three 2" water-cooled cathodes, RF/DC power, ideal for various materials.
High-Vacuum, Double-Magnetron Target Sputter Coater/ Thermal Evaporator - DST2-TG
High Vacuum Double Magnetron Target Sputter Coater/Thermal Evaporator DST2-TG. Compact unit for thermal evaporation and sputtering. Wi-Fi control, touch screen, high vacuum environment, ideal for diverse coatings in glove box settings.
PLD Pulsed Laser Deposition System
Pulsed Laser Deposition and Thermal Evaporator system - PLD-T is a high vacuum thin film deposition system enables to deposit different materials by both Pulsed Laser Deposition and thermal evaporation technique.
Turbo Pumped Carbon Coater and Thermal Evaporator – DCT-T-300
Turbo Pumped Carbon Coater and Thermal Evaporator – DCT-T-300 is equipped with a large chamber, making it perfect for preparing...
Large Desk Turbo-Pumped Carbon Coater – DCT-300
The Large Desk Turbo-Pumped Carbon Coater – DCT-300 system with a spacious chamber, perfect for prepping samples...
DC Power Supplies for Magnetron Sputtering & Plasma Generators
DC Power Supplies for Magnetron Sputtering & Plasma Generators designed for magnetron sputtering and plasma generation offer reliable solutions for both industrial and...
RF Radio Frequency Plasma Generators
RF Radio Frequency Plasma Generators create controlled plasma, ideal for semiconductor manufacturing and material processing. These devices offer precise ionization control...
Plasma Cleaner & Reaction Systems
Torontech delivers advanced plasma systems and supplies, offering state-of-the-art solutions for precise processing across multiple industries. Our high-quality equipment is designed...
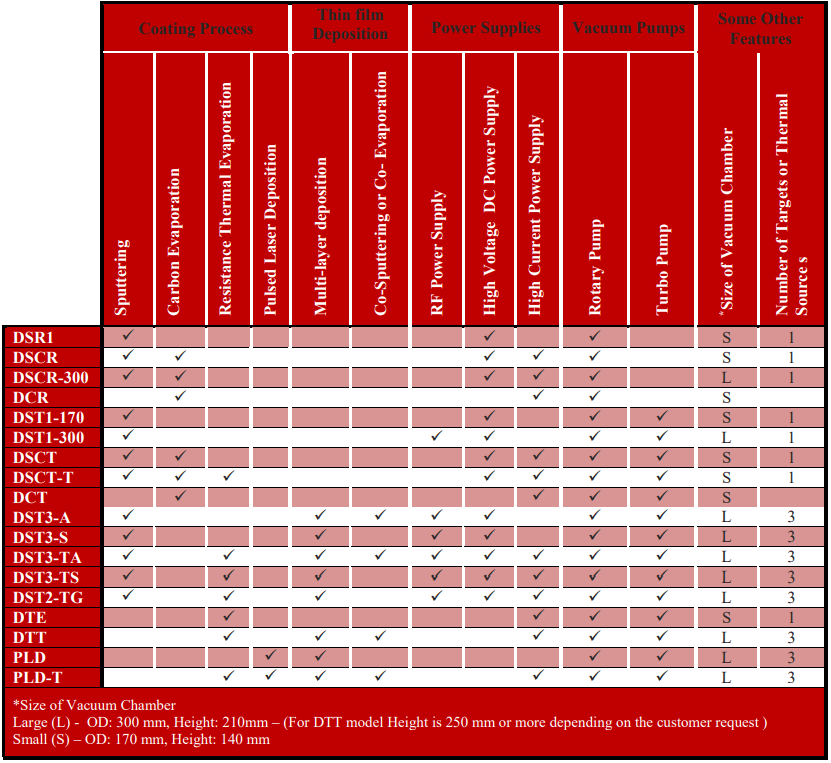